Hello Neil!
Wow thank you as usual for your exceptional explanation and the examples.
To get to your questions directly:
Is this what you are looking for?
Basically yes. My model as I said, will be a Cube satellite, with motor drive inertias, and as such (beyond the sphereical joint) what you've modelled is pretty much what each sub system (motor, controller and rotor) will end up being.
Why do you want to use a "mathematical motor"?
This probably requires some more explanation. To be frank, it's mostly because I don't know how to use those finished models.
In the real system, I am using a EC 45 Flat motor (251601) plus their current controller (see attached PDF) from maxon motor. With the controller, I can drive the motor with a current source. Their data sheet has quite a bit of information about the motor itself, however when attempting to use the built-in model SM_PermanentMagnet
and the subsequent example SMPM_CurrentSouce
which at the time I assumed would be a perfect starting point.
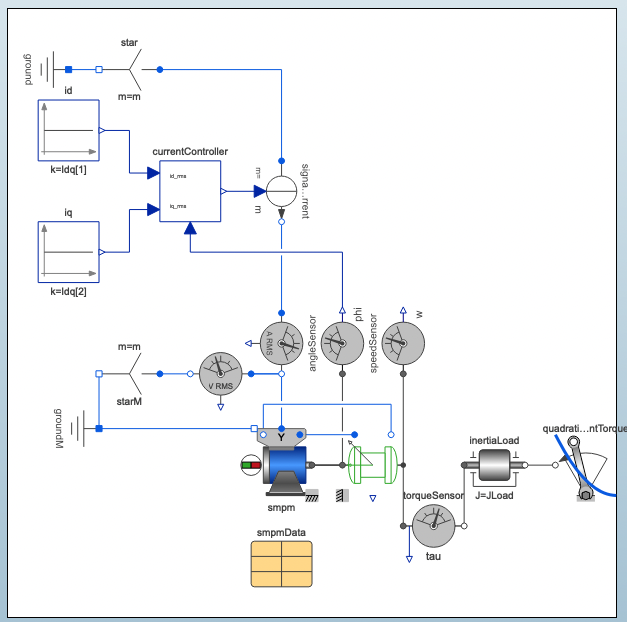
I am completely overwhelmed with how it's set up and how to give correct data compared to my real life motor and controller, that I can actually do anything with. Lmd and Lmq, LD and LQ values and most other variables which work in the example, are vastly different to the values from the data sheet and I have no current way to measure or figure them out myself, maxon as a company also refuses to give anything more than the public facing catalogue data.
However, my mathematical ODE model represents the motors with their controller quite accurately, which I've verified and used for this project (https://www.youtube.com/watch?v=Lzw3ZGTuMUU) (which is one of the walls of the cube sat), and since I already had a model that does what I wanted, I decided it was the fastest route, rather than trying to hack the examples together.
I would absolutely appreciate if you could show me an example of how to improve my model with the rotational flanges, or to make it more physical in any other way. When attempting myself, I realise now that mixing and matching different blocks isn't as easy as I'd hope. The rotational flange only accepts rotational connections it seems...
As as side question, Do you have any suggestions for material, tutorials or likewise for the 'modelica method' you mention? It's difficult to find literature that is suited for beginners for this modeling concept, and my only experience as you accurately deduced, is simulink, which clearly isn't appropriate.
Thank you again for the detailed answer, I very much appreciate the help.
Attachments: